about his new house and garage.
I figured I'd follow up.
Last weekend (12/11-12/13) my dad and I and a friend installed a rolling door on my garage. The garage is a detached 22x30 (interior) building with a 9x16 car door and separate man door. It has its own electric meter and panel, but currently is only wired for 110V power. I'll be wiring up for 220 as my garage build progresses.
Pics of the door installation:





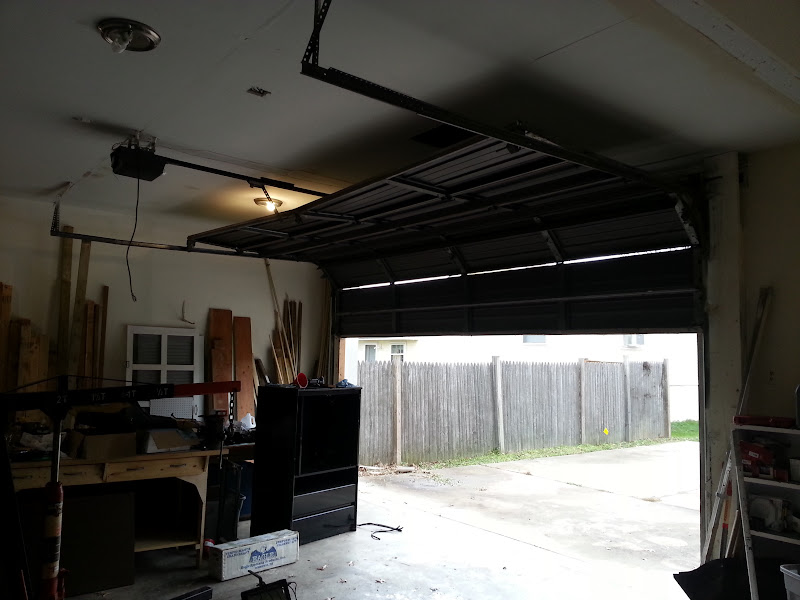
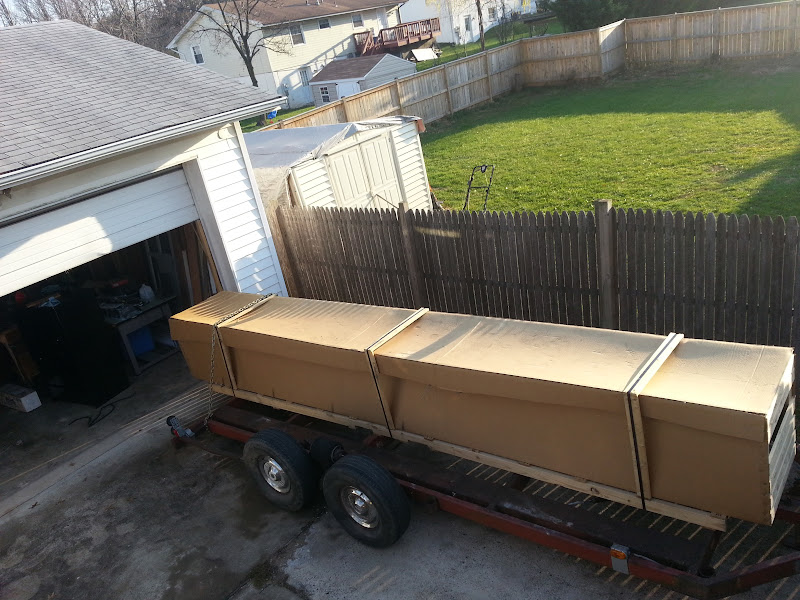
For the heavy lifting

Door in a box

Tine extensions to reach far enough into the garage to do the job

Why no, I'm not compensating for anything...



First: get the old door out. Here we used the forklift to take the weight so we could unhook the springs.

Next, propping up the next higher panel so we could unbolt the one below
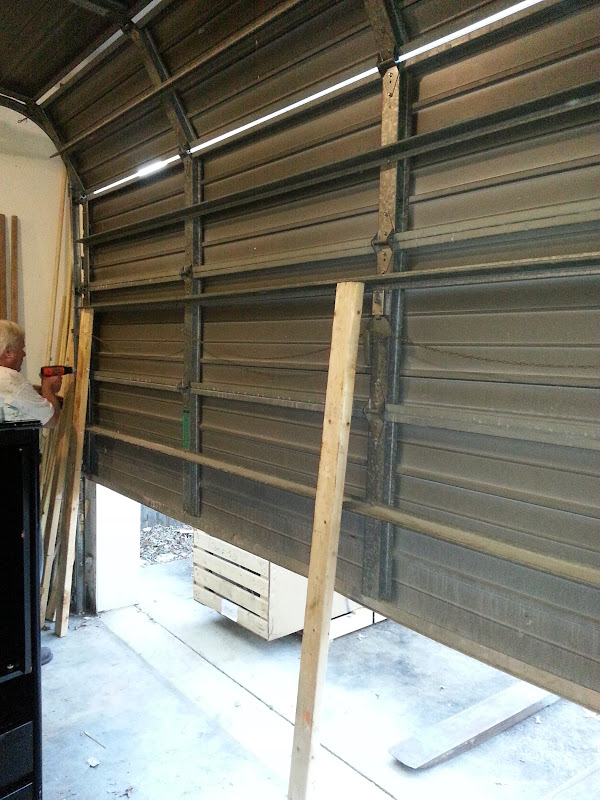
Aaaaannnnd it's out

It's tough to get good shots of the tracks installed. This is actually where we spent most of the *time* required... figuring out what in the building we could anchor to securely, drilling clearance and pilot holes for 3/8 x 7" lag screws and turning them in.
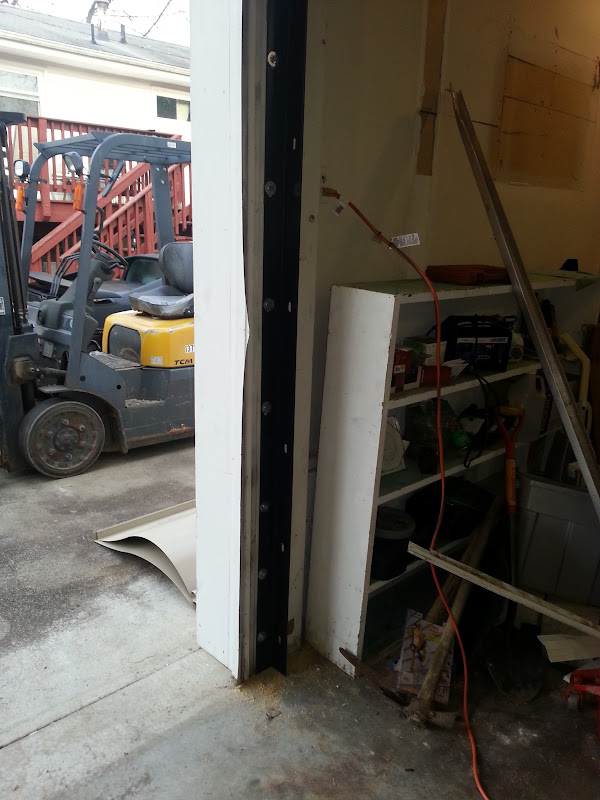
The installer or builder had set up a stack of 2x10's on each jamb, but it wasn't clear how well they were anchored to the actual load bearing members of the building. Here we had to cut and install some blocks at the top of one in order to be able to put lags through into the top plate of the wall, which of course is anchored to the roof trusses (we hope).



Per the spec sheet included with the unit, the curtain assembly, here shown elevated for installation, weighs 519 lbs. It's secured to the tracks by three 1/2" bolts per side.

Bolted up... didn't even fall on anyone's head
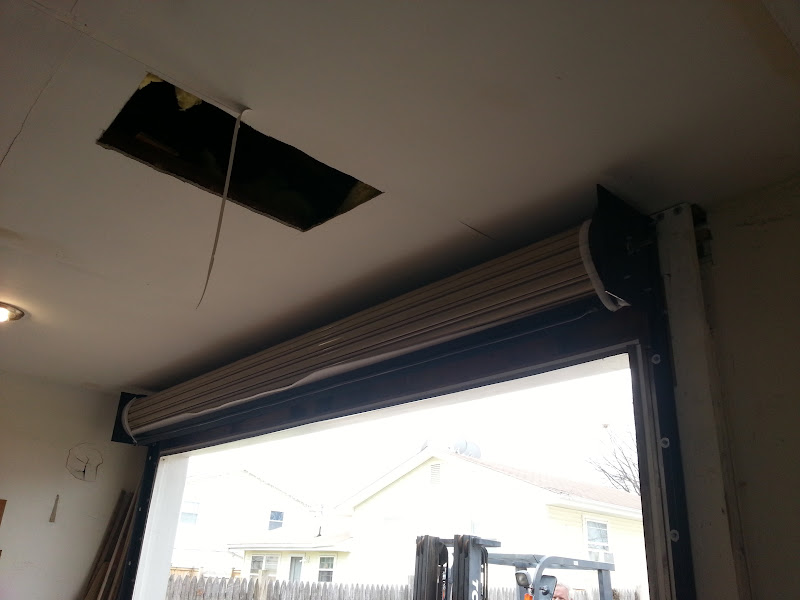
Skip a couple of steps...
Here it is installed, with the manual operator assembled

AAAAAAANNNNNNNDDDDDD... the finished product:

They'll even let me advertise to myself for FREE!

Wouldn't be finished without extra parts (Wait... what?)

The reason I went to all that trouble and threw down about twice the cash that a sectional garage door would cost is to free up ceiling space for the installation of a FUCKING BRIDGE CRANE, BITCHES.

More to follow on that. I was expecting to have to build the rails from 4" I-beams and beam trolleys, anchored to the roof trusses through the ceiling, with the bridge being a 4" beam with a T-section welded to the top so it could hold 1,000# in the middle of a 20 foot span. This should be a very compact arrangement and let me get my hook height as high as possible under the 10'8" ceiling.
However, the place from which my dad is semi-retired assembles Ingersol Rand trolleys and rails and the owner offered some to my dad for FREE!.
I probably won't be able to keep the hook quite as high with these materials, but the price is right. Even without the free stuff, the crane was going to be MUCH cheaper to build than the door was to buy.