The Mule rides again (sort of) - pics.
Moderators: The Dark Side of Will, Series8217
- Series8217
- 1988 Fiero Track Car
- Posts: 6078
- Joined: Thu Jun 02, 2005 9:47 pm
- Location: Los Angeles, CA
Re: The Mule rides again (sort of) - pics.
Are you sure it's not the brake booster flexing?
On my 88 I get 0.035" vertical deflection of the brake master cylinder with full pedal force. As much as I can generate. 150 lbs? 200 lbs?
This is with the stock firewall but obviously not the stock master or booster.
On my 88 I get 0.035" vertical deflection of the brake master cylinder with full pedal force. As much as I can generate. 150 lbs? 200 lbs?
This is with the stock firewall but obviously not the stock master or booster.
-
- Peer Mediator
- Posts: 15750
- Joined: Wed Nov 24, 2004 11:13 pm
- Location: In the darkness, where fear and knowing are one
- Contact:
Re: The Mule rides again (sort of) - pics.
There are quite a few chassis that have similar issues. In many front engine cars, the far end of the brake MC can be braced to the shock or strut tower effectively, but that doesn't work in a Fiero.ericjon262 wrote: ↑Wed May 01, 2024 9:13 pm
apparently plates like that are a thing on third gen F bodies, and a bunch of guys are happy with the results.
https://www.thirdgen.org/forums/organiz ... brace.html
this is definitely worth keeping more in mind than I thought.
Maybe it is? Might be time for the Tesla electric booster conversion.Series8217 wrote: ↑Fri May 03, 2024 3:59 pm Are you sure it's not the brake booster flexing?
On my 88 I get 0.035" vertical deflection of the brake master cylinder with full pedal force. As much as I can generate. 150 lbs? 200 lbs?
This is with the stock firewall but obviously not the stock master or booster.
I need the plate as a way to mount both a clutch pedal stop and my DBW throttle pedal, so I'll finish it up anyway.
-
- Posts: 3082
- Joined: Mon May 24, 2010 5:34 pm
- Location: Aiken, SC
Re: The Mule rides again (sort of) - pics.
Series8217 wrote: ↑Fri May 03, 2024 3:59 pm Are you sure it's not the brake booster flexing?
On my 88 I get 0.035" vertical deflection of the brake master cylinder with full pedal force. As much as I can generate. 150 lbs? 200 lbs?
did you check horizontal deflection too? this is an interesting observation, I know in my car, it appears as though the master moves a significant amount as I bleed the brakes.
I've seen several bracing methods, but without connecting the front wheelwells to the front frunk wall, I'm not sure there's anything there to really stop movement. I have a few ideas I would like to explore, but I am very intrigued by Series' posted information above, maybe I need to get an indicator out too...The Dark Side of Will wrote: ↑Fri May 03, 2024 4:37 pmThere are quite a few chassis that have similar issues. In many front engine cars, the far end of the brake MC can be braced to the shock or strut tower effectively, but that doesn't work in a Fiero.ericjon262 wrote: ↑Wed May 01, 2024 9:13 pm
apparently plates like that are a thing on third gen F bodies, and a bunch of guys are happy with the results.
https://www.thirdgen.org/forums/organiz ... brace.html
this is definitely worth keeping more in mind than I thought.
The "Tesla" booster is also in several other cars too, it's made by bosch, and accords got them too. That said, you posted in that thread so you already knew that...The Dark Side of Will wrote: ↑Fri May 03, 2024 4:37 pmMaybe it is? Might be time for the Tesla electric booster conversion.Series8217 wrote: ↑Fri May 03, 2024 3:59 pm Are you sure it's not the brake booster flexing?
On my 88 I get 0.035" vertical deflection of the brake master cylinder with full pedal force. As much as I can generate. 150 lbs? 200 lbs?
This is with the stock firewall but obviously not the stock master or booster.
I need the plate as a way to mount both a clutch pedal stop and my DBW throttle pedal, so I'll finish it up anyway.
https://www.realfierotech.com/viewtopic ... er#p161121
"I am not what you so glibly call to be a civilized man. I have broken with society for reasons which I alone am able to appreciate. I am therefore not subject to it's stupid laws, and I ask you to never allude to them in my presence again."
- Series8217
- 1988 Fiero Track Car
- Posts: 6078
- Joined: Thu Jun 02, 2005 9:47 pm
- Location: Los Angeles, CA
Re: The Mule rides again (sort of) - pics.
0.016" horizontal deflection.ericjon262 wrote: ↑Sat May 04, 2024 5:18 pmSeries8217 wrote: ↑Fri May 03, 2024 3:59 pm Are you sure it's not the brake booster flexing?
On my 88 I get 0.035" vertical deflection of the brake master cylinder with full pedal force. As much as I can generate. 150 lbs? 200 lbs?
did you check horizontal deflection too? this is an interesting observation, I know in my car, it appears as though the master moves a significant amount as I bleed the brakes.
I have the stock Fiero pedal box with an E90 M3 brake booster and master. The adapter that consists of a steel tube and two flanges -- one with the Fiero 4-hole pattern and the other with the E90 2-hole pattern. The ABS module is connected via braided steel lines so the pipes aren't providing any additional bracing.
-
- Posts: 3082
- Joined: Mon May 24, 2010 5:34 pm
- Location: Aiken, SC
Re: The Mule rides again (sort of) - pics.
I had a second, so I measured the deflection of mine as well, I'm getting around .020 vertical, I probably could have pushed the pedal a bit harder, but it seemed to deflect to .020 and then stop flexing.
"I am not what you so glibly call to be a civilized man. I have broken with society for reasons which I alone am able to appreciate. I am therefore not subject to it's stupid laws, and I ask you to never allude to them in my presence again."
- Series8217
- 1988 Fiero Track Car
- Posts: 6078
- Joined: Thu Jun 02, 2005 9:47 pm
- Location: Los Angeles, CA
Re: The Mule rides again (sort of) - pics.
Wow! On the '88 there is a steel brace that goes from the base flange of the master cylinder to the combo valve, which is bolted through to the left frame rail. Do you have that? I eliminated it with my master cylinder swap... I might need to bring it back...
-
- Peer Mediator
- Posts: 15750
- Joined: Wed Nov 24, 2004 11:13 pm
- Location: In the darkness, where fear and knowing are one
- Contact:
Re: The Mule rides again (sort of) - pics.
After wildly missing my end of June goal due to the Jeep taking WAY more time than I thought, I was able to get back to The Mule 2 of the last 3 weekends. I looked over my fit check list, then dropped the engine back out to finish up the harness.
I trimmed the right hinge box to give "just enough" clearance with the engine in place.
As it appeared in the last photo + the upper scribe line 1/2" from the old position of the cam cover and the lower scribe line about 1/4":

Cut along the lower scribe line:

Finally have *juuuuuuuust* enough:


Probably will want to increase it for dynamic clearance, but this lets me fit the engine.
I trimmed the 90 degree elbow off the oil cooler and ended up with greater clearance to the AC lines than I'd had with the prior 120 degree elbow, so that's an improvement. I have a 60 degree elbow (120 degree bend) to look at as well.


I was also able to scope out clearance to the '85-'86 style heater tubes with the smaller CS130 alternator installed.

There does not appear to be any satisfactory way to make that work. As shown, the hoses are out of the way, but there's not even a fingertip of clearance between the tube and the mount bracket... and everything is packed into that little space as the heater tubes try to snake around the "shelf" low on the firewall.
I also found that rotating the engine down around the forward cradle bolts drags the connector position assurance (CPA) guard feature on the cam sensor connector against the frame rail. This actually cracked the guard, but that means it did its job in protecting the CPA clip.

I installed and refreshed my memory on what my custom AC lines look like and how they fit. The low side line passes through a loop of the '85-'86 fuel tank vent line, which is undesirable, but not prohibitive. I'm thinking about which pieces of tubing, between the Storm Trooper and The Mule, I need to send off to Inline Tube for reverse engineering. Or maybe just have them 3D scanned?
I also looked at O2 sensor wiring and general harness construction and thermal protection. I think I have that figured out, but need to do some figuring and order some fire sleeve.
When I re-routed my AC lines, I did so for packaging and clearance reasons. I'm thinking I'll have to do the same for the heater lines. The Northstar heater connections are at the LF and LR corners of the engine, as installed. The Fiero heater connections are at the RF corner of the engine bay, regardless of whether the '85-'86 (as I have done) or '87-'88 lines are installed. This means that no matter what, additional plumbing has to wrap around the engine bay.
With the heater return to the waterpump capped, and the heater return from the heater core T'd into the right side coolant pipe, the car takes about 3 times as long to start to deliver heat to the occupants as it does when the return from the heater core is plumbed to the heater return to the waterpump, so there aren't shortcuts in heater plumbing without reworking flow inside the waterpump.
If I cut and bead the heater tubes right where they come out from under the floor pan, then I can run hoses directly from there and do not have to try to find the perfect way to squeeze those lines between the forward engine mount bracket and the "shelf" across the firewall.
If I cut the heater tubes, I might as well swap the '87 heater tubes back into the car.
Instead of running hoses across the bottom of the engine bay, cutting vertical holes through the firewall shelf might work out well... that gets the heater hoses above the shelf where they're no longer competing for space with the AC hoses and oil cooler and oil cooler hoses, but does not require sneaking the heater hoses between the shelf and the engine. I'll have to take a look at that when I'm back at the car. If I do that, then those holes will have to route around the tubes to the fuel tank expansion volume... which I *do* have in SS from Inline Tube
My Samco silicone hose order arrived. 4 meters each of 5/8" (16mm, green), 3/4" (19mm, green), 5/16" (8mm, red) & 3/8" (9.5mm,red), with the red ones being lined so they can handle pressurized fuel. With that batch plus a couple of elbows and joiners to play with... Dam Str8 I deserve a free keychain!

I trimmed the right hinge box to give "just enough" clearance with the engine in place.
As it appeared in the last photo + the upper scribe line 1/2" from the old position of the cam cover and the lower scribe line about 1/4":

Cut along the lower scribe line:

Finally have *juuuuuuuust* enough:


Probably will want to increase it for dynamic clearance, but this lets me fit the engine.
I trimmed the 90 degree elbow off the oil cooler and ended up with greater clearance to the AC lines than I'd had with the prior 120 degree elbow, so that's an improvement. I have a 60 degree elbow (120 degree bend) to look at as well.


I was also able to scope out clearance to the '85-'86 style heater tubes with the smaller CS130 alternator installed.

There does not appear to be any satisfactory way to make that work. As shown, the hoses are out of the way, but there's not even a fingertip of clearance between the tube and the mount bracket... and everything is packed into that little space as the heater tubes try to snake around the "shelf" low on the firewall.
I also found that rotating the engine down around the forward cradle bolts drags the connector position assurance (CPA) guard feature on the cam sensor connector against the frame rail. This actually cracked the guard, but that means it did its job in protecting the CPA clip.

I installed and refreshed my memory on what my custom AC lines look like and how they fit. The low side line passes through a loop of the '85-'86 fuel tank vent line, which is undesirable, but not prohibitive. I'm thinking about which pieces of tubing, between the Storm Trooper and The Mule, I need to send off to Inline Tube for reverse engineering. Or maybe just have them 3D scanned?
I also looked at O2 sensor wiring and general harness construction and thermal protection. I think I have that figured out, but need to do some figuring and order some fire sleeve.
When I re-routed my AC lines, I did so for packaging and clearance reasons. I'm thinking I'll have to do the same for the heater lines. The Northstar heater connections are at the LF and LR corners of the engine, as installed. The Fiero heater connections are at the RF corner of the engine bay, regardless of whether the '85-'86 (as I have done) or '87-'88 lines are installed. This means that no matter what, additional plumbing has to wrap around the engine bay.
With the heater return to the waterpump capped, and the heater return from the heater core T'd into the right side coolant pipe, the car takes about 3 times as long to start to deliver heat to the occupants as it does when the return from the heater core is plumbed to the heater return to the waterpump, so there aren't shortcuts in heater plumbing without reworking flow inside the waterpump.
If I cut and bead the heater tubes right where they come out from under the floor pan, then I can run hoses directly from there and do not have to try to find the perfect way to squeeze those lines between the forward engine mount bracket and the "shelf" across the firewall.
If I cut the heater tubes, I might as well swap the '87 heater tubes back into the car.
Instead of running hoses across the bottom of the engine bay, cutting vertical holes through the firewall shelf might work out well... that gets the heater hoses above the shelf where they're no longer competing for space with the AC hoses and oil cooler and oil cooler hoses, but does not require sneaking the heater hoses between the shelf and the engine. I'll have to take a look at that when I'm back at the car. If I do that, then those holes will have to route around the tubes to the fuel tank expansion volume... which I *do* have in SS from Inline Tube

My Samco silicone hose order arrived. 4 meters each of 5/8" (16mm, green), 3/4" (19mm, green), 5/16" (8mm, red) & 3/8" (9.5mm,red), with the red ones being lined so they can handle pressurized fuel. With that batch plus a couple of elbows and joiners to play with... Dam Str8 I deserve a free keychain!


-
- Posts: 3082
- Joined: Mon May 24, 2010 5:34 pm
- Location: Aiken, SC
Re: The Mule rides again (sort of) - pics.
looks good!, I have to say though, as a maintenance technician, I see the clearance to the hinge box and cringe, one day, you'll need to pick the motor up just a smidge, and you won't have a smidge to move it unless you open that up some more, it can be done cleanly and not look like a disaster...
is your cam sensor one molded part, or a molded part with a metal clip? you may be able to remove the clip and rotate the sensor 180 degrees so the connector points the other direction. that said, it looks like the bolt won't allow for that. maybe you can do the fancy racecar thing I don't understand, and solder wires to the terminals in the sensor, fill it with epoxy and terminate the connector further away?
is your cam sensor one molded part, or a molded part with a metal clip? you may be able to remove the clip and rotate the sensor 180 degrees so the connector points the other direction. that said, it looks like the bolt won't allow for that. maybe you can do the fancy racecar thing I don't understand, and solder wires to the terminals in the sensor, fill it with epoxy and terminate the connector further away?
"I am not what you so glibly call to be a civilized man. I have broken with society for reasons which I alone am able to appreciate. I am therefore not subject to it's stupid laws, and I ask you to never allude to them in my presence again."
-
- Peer Mediator
- Posts: 15750
- Joined: Wed Nov 24, 2004 11:13 pm
- Location: In the darkness, where fear and knowing are one
- Contact:
Re: The Mule rides again (sort of) - pics.
Yeah, totally get it. I also don't think my engine is staked down quite firmly enough that I can get away with 1/8" of top side clearanceericjon262 wrote: ↑Mon Sep 02, 2024 9:40 pm looks good!, I have to say though, as a maintenance technician, I see the clearance to the hinge box and cringe, one day, you'll need to pick the motor up just a smidge, and you won't have a smidge to move it unless you open that up some more, it can be done cleanly and noYt look like a disaster...

Unplugging the connector before I swing the cradle would probably be fine. It has a fixed orientation, so unplugging it is really the only option short of removing the sensor entirely... which is at best quite awkward with the engine in the car.ericjon262 wrote: ↑Mon Sep 02, 2024 9:40 pm is your cam sensor one molded part, or a molded part with a metal clip? you may be able to remove the clip and rotate the sensor 180 degrees so the connector points the other direction. that said, it looks like the bolt won't allow for that. maybe you can do the fancy racecar thing I don't understand, and solder wires to the terminals in the sensor, fill it with epoxy and terminate the connector further away?
OE connectors are quite reliable... for their design range of mate/demate cycles. The fancy racecar connectors remain reliable for much higher cycle counts. If you start with new socket contacts in the connector, mate the connector once and ziptie/shrink tube it in place, it should be as reliable as the fancy racecar connector. Then the fancy racecar connector can be a few inches of wiring away and will be the disconnect location for harness maintenance or sensor replacement.
-
- Peer Mediator
- Posts: 15750
- Joined: Wed Nov 24, 2004 11:13 pm
- Location: In the darkness, where fear and knowing are one
- Contact:
Re: The Mule rides again (sort of) - pics.
Got to the point of taking photos of my recent engine bay packaging updates.




And here's what I was really aiming for:

That removes the heater pipes from the gap between the firewall shelf and the engine mount bracket, creating more space all around.

Now that the holes are cut, deburred, cleaned, painted & grommeted, I can install the placeholder tubes as shown. Next step is to cut, deburr, blast/strip, bead & paint/coat the original '87 tubes that came out of the car and install those with some extra SamCo elbows. The angle between the under-car tubes and the pass-through tubes is right at 120 degrees, so a 60 degree elbow is perfect to connect the two. The '87 tube set swaps the places of the supply & return, so now my bright green 120 degree elbow is cut wrong and I have to replace it--although I'll probably go to 90's at those locations now.
This is my other problem:

That's my bespoke refrigerant return line passing through a loop in the '85-'86 four cylinder fuel vapor line that goes up to the vapor canister on the left side of the engine bay.
These two are the '87-'88 fuel tank expansion volume lines. The upper one in frame (larger diameter) connects the fuel sending unit vent line to the bottom of the expansion volume. The other line (smaller diameter) connects the top of the expansion volume to the looped vapor canister line in the photo above.

There's 6 feet of extra tube in the car because the expansion volume is above the right wheel house and the vapor canister is on the left side of the engine bay. I realized I could eliminate the 6 feet of extra tube by relocating the vapor canister to the right side of the engine bay. That would also eliminate my packaging problem between the AC return line and the fuel vent line.
Since the rest of my system is 2006 Corvette, I started off looking at the 2006 Corvette vapor canister. It's a blocky thing that's shared across most of GM's contemporary car lines. I was able to get Dorman to send me dimensions so I didn't have to grab one for a fit check. Unfortunately, it's just too large to tuck under or in front of the battery tray. I was lamenting the loss of the "easy way" when I realized I could mount a vapor canister OUTSIDE the body metal in the right wheel house, just below the fuel tank expansion volume. This gets it out of the engine bay completely and there is, relatively speaking a LOT of room for it. Now I just need to figure out which one I'm going to use. The Corvette bracket mounts it sort of diagonally, so I'll probably want a bracket from something else... just have to figure out what.
So there you have it: the three major fitment challenges I still had are solved.




And here's what I was really aiming for:

That removes the heater pipes from the gap between the firewall shelf and the engine mount bracket, creating more space all around.

Now that the holes are cut, deburred, cleaned, painted & grommeted, I can install the placeholder tubes as shown. Next step is to cut, deburr, blast/strip, bead & paint/coat the original '87 tubes that came out of the car and install those with some extra SamCo elbows. The angle between the under-car tubes and the pass-through tubes is right at 120 degrees, so a 60 degree elbow is perfect to connect the two. The '87 tube set swaps the places of the supply & return, so now my bright green 120 degree elbow is cut wrong and I have to replace it--although I'll probably go to 90's at those locations now.
This is my other problem:

That's my bespoke refrigerant return line passing through a loop in the '85-'86 four cylinder fuel vapor line that goes up to the vapor canister on the left side of the engine bay.
These two are the '87-'88 fuel tank expansion volume lines. The upper one in frame (larger diameter) connects the fuel sending unit vent line to the bottom of the expansion volume. The other line (smaller diameter) connects the top of the expansion volume to the looped vapor canister line in the photo above.

There's 6 feet of extra tube in the car because the expansion volume is above the right wheel house and the vapor canister is on the left side of the engine bay. I realized I could eliminate the 6 feet of extra tube by relocating the vapor canister to the right side of the engine bay. That would also eliminate my packaging problem between the AC return line and the fuel vent line.
Since the rest of my system is 2006 Corvette, I started off looking at the 2006 Corvette vapor canister. It's a blocky thing that's shared across most of GM's contemporary car lines. I was able to get Dorman to send me dimensions so I didn't have to grab one for a fit check. Unfortunately, it's just too large to tuck under or in front of the battery tray. I was lamenting the loss of the "easy way" when I realized I could mount a vapor canister OUTSIDE the body metal in the right wheel house, just below the fuel tank expansion volume. This gets it out of the engine bay completely and there is, relatively speaking a LOT of room for it. Now I just need to figure out which one I'm going to use. The Corvette bracket mounts it sort of diagonally, so I'll probably want a bracket from something else... just have to figure out what.
So there you have it: the three major fitment challenges I still had are solved.
-
- Peer Mediator
- Posts: 15750
- Joined: Wed Nov 24, 2004 11:13 pm
- Location: In the darkness, where fear and knowing are one
- Contact:
Re: The Mule rides again (sort of) - pics.
Oddly enough, the 2006 Chevy Express has a vapor canister very similar to the 2006 Corvette's, but clips into a plastic bracket that can mount on a flat surface. This one might be a winner.
Edit: An interesting tidbit is that the 2014 Corvette vapor canister appears to have the three terminal fuel tank pressure sensor built into it instead of into the fuel sender or fill plumbing. That probably saves GM 30 feet of 22ga wire per vehicle having that sensor near the engine bay and ECM instead of back at the fuel tank. It's completely different than prior designs, and the bracket is really wild. If I used that, I'd have to buy it and cut it up, but at least it's not very expensive. RockAuto lists some of the brackets as well and for significantly lower prices than the usual network of look-a-like GM parts vendors.
Edit: An interesting tidbit is that the 2014 Corvette vapor canister appears to have the three terminal fuel tank pressure sensor built into it instead of into the fuel sender or fill plumbing. That probably saves GM 30 feet of 22ga wire per vehicle having that sensor near the engine bay and ECM instead of back at the fuel tank. It's completely different than prior designs, and the bracket is really wild. If I used that, I'd have to buy it and cut it up, but at least it's not very expensive. RockAuto lists some of the brackets as well and for significantly lower prices than the usual network of look-a-like GM parts vendors.
-
- Posts: 3082
- Joined: Mon May 24, 2010 5:34 pm
- Location: Aiken, SC
Re: The Mule rides again (sort of) - pics.
I like the heater tube mod, it's a pretty clean way to reduce bulk in the engine bay. nice work!
I'd like to see more details on the vapor canister.
I'd like to see more details on the vapor canister.
I gave this further consideration, and there's something that hasn't been mentioned, if you push hard on the brake pedal, and also push yourself into the seat, it could be perceived as the MC and firewall deflecting, when the actual deflection is taking place in the seat.Series8217 wrote: ↑Fri May 03, 2024 3:59 pm Are you sure it's not the brake booster flexing?
On my 88 I get 0.035" vertical deflection of the brake master cylinder with full pedal force. As much as I can generate. 150 lbs? 200 lbs?
This is with the stock firewall but obviously not the stock master or booster.
20240503_125506.jpg
20240503_125526.jpg
"I am not what you so glibly call to be a civilized man. I have broken with society for reasons which I alone am able to appreciate. I am therefore not subject to it's stupid laws, and I ask you to never allude to them in my presence again."
-
- Peer Mediator
- Posts: 15750
- Joined: Wed Nov 24, 2004 11:13 pm
- Location: In the darkness, where fear and knowing are one
- Contact:
Re: The Mule rides again (sort of) - pics.
Thanks!ericjon262 wrote: ↑Sat Oct 05, 2024 8:06 pm I like the heater tube mod, it's a pretty clean way to reduce bulk in the engine bay. nice work!
I'd like to see more details on the vapor canister.
Yeah, I'll post more about the canister as I get it figured out.
My hot take is that human proprioception isn't really dealing with squishiness in the seat. We don't really feel small displacements... we feel force much more effectively.ericjon262 wrote: ↑Sat Oct 05, 2024 8:06 pmI gave this further consideration, and there's something that hasn't been mentioned, if you push hard on the brake pedal, and also push yourself into the seat, it could be perceived as the MC and firewall deflecting, when the actual deflection is taking place in the seat.Series8217 wrote: ↑Fri May 03, 2024 3:59 pm Are you sure it's not the brake booster flexing?
On my 88 I get 0.035" vertical deflection of the brake master cylinder with full pedal force. As much as I can generate. 150 lbs? 200 lbs?
This is with the stock firewall but obviously not the stock master or booster.
20240503_125506.jpg
20240503_125526.jpg
The problem is linearity & modulation in the brake pedal response. FieroGuru's data shows that most of the loss of linearity probably comes from overdriving the factory booster. Beyond the input limit resulting in max output, there's no additional boost, so the response noses over and becomes non-linear. That's a function of high pedal loads required by tiny stock brakes, the limits of the stock small-diameter single-diaphragm booster and, for a minority of the effect, flex in the system at high pedal loads.
Since I'd already started the design and had done a couple of iterations, I thought I'd go ahead and mitigate the firewall flex. As previously noted, the firewall stiffener also gives me a good way to mount the clutch pedal stop that the 7.25" clutch requires and DBW pedal sensor.
-
- Peer Mediator
- Posts: 15750
- Joined: Wed Nov 24, 2004 11:13 pm
- Location: In the darkness, where fear and knowing are one
- Contact:
Re: The Mule rides again (sort of) - pics.
This was incorrectly listed for my CRD Heep, but may have relevance to The Mule: https://www.rockauto.com/en/moreinfo.ph ... 9&jsn=1948
My current accessory bracket retains the Cadillac tensioner... which is BRUTALLY stiff. The tensioners for my diesel Jeep and diesel Benz are outright soft by comparison.
The difference? Both of those applications have decoupler pulleys on their alternators. A decoupler pulley has a roller clutch built in which allows the engine to accelerate the alternator, but not decelerate it. Diesels have high alternator drive ratios so that they can keep their alternators in the alternators' useful RPM ranges despite the diesel's lower redline RPM compared to a gasoline engine. When a diesel at WOT spins out to 4300 RPM before a shift, the alternator might be turning 17,200 RPM. In the case of the 722.6 1-2 shift, engine RPM drops 39% to 2600. This means that the alternator has to come down to 10,400... a drop of nearly 7000 RPM and dissipation of a bit over 64% of the alternator's kinetic energy. With a solid pulley, the belt and tensioner must pull the alternator RPM down, absorbing the power related to that deceleration. This creates a high likelihood of chirping the belt. Preventing the belt from chirping requires an extremely stiff tensioner to generate enough friction at the belt-to-pulley interface to transfer the alternator's kinetic energy to the crankshaft at the power level required by the rate of engine deceleration. With a decoupled pulley, the alternator spins down on its own and does not have to be pulled down by the belt drive. This means a belt drive that uses a decoupled alternator can operate with a much softer tensioner than one that uses a solid pulley. The softer tensioner reduces tension on the belt and lateral load on the bearings of every pulley in the accessory drive, thereby increasing both belt and accessory bearing life.
Thus I am constantly somewhat on the lookout for a decoupled alternator pulley in order run a softer tensioner on The Mule, and for the tensioner itself.
My current accessory bracket retains the Cadillac tensioner... which is BRUTALLY stiff. The tensioners for my diesel Jeep and diesel Benz are outright soft by comparison.
The difference? Both of those applications have decoupler pulleys on their alternators. A decoupler pulley has a roller clutch built in which allows the engine to accelerate the alternator, but not decelerate it. Diesels have high alternator drive ratios so that they can keep their alternators in the alternators' useful RPM ranges despite the diesel's lower redline RPM compared to a gasoline engine. When a diesel at WOT spins out to 4300 RPM before a shift, the alternator might be turning 17,200 RPM. In the case of the 722.6 1-2 shift, engine RPM drops 39% to 2600. This means that the alternator has to come down to 10,400... a drop of nearly 7000 RPM and dissipation of a bit over 64% of the alternator's kinetic energy. With a solid pulley, the belt and tensioner must pull the alternator RPM down, absorbing the power related to that deceleration. This creates a high likelihood of chirping the belt. Preventing the belt from chirping requires an extremely stiff tensioner to generate enough friction at the belt-to-pulley interface to transfer the alternator's kinetic energy to the crankshaft at the power level required by the rate of engine deceleration. With a decoupled pulley, the alternator spins down on its own and does not have to be pulled down by the belt drive. This means a belt drive that uses a decoupled alternator can operate with a much softer tensioner than one that uses a solid pulley. The softer tensioner reduces tension on the belt and lateral load on the bearings of every pulley in the accessory drive, thereby increasing both belt and accessory bearing life.
Thus I am constantly somewhat on the lookout for a decoupled alternator pulley in order run a softer tensioner on The Mule, and for the tensioner itself.
-
- Peer Mediator
- Posts: 15750
- Joined: Wed Nov 24, 2004 11:13 pm
- Location: In the darkness, where fear and knowing are one
- Contact:
Re: The Mule rides again (sort of) - pics.
The injectors I'm using are for the LC3 factory supercharged Northstar. I know GM intended them for a high power 4V engine, and that engine has similar port geometry to my engine. Spray pattern should be about as good as it can be for a hot rod fitment. I started off with Bosch EV6 connectors for the injectors because I was having a hard time finding info on Aptiv (Delphi) EV6 connectors. I eventually found the PNs for the Delphi connectors. The Delphi connectors are GT150 series that have individual wire seals and a terminal position assurance (TPA) part that clips onto the connector body and has projections that push against the outside of the wire seals to block egress of the terminals. Of course this ensures that even if the main latch is released or breaks, the terminals won't back out of the connector far enough to break the circuit. ProWire designed and manufactured their own TPA for these connectors. The ProWire TPA includes a booting lip, which the factory part does not. Obvi ProWire also sells a boot that works with that booting lip.
TPA: https://www.prowireusa.com/TPA-EV14
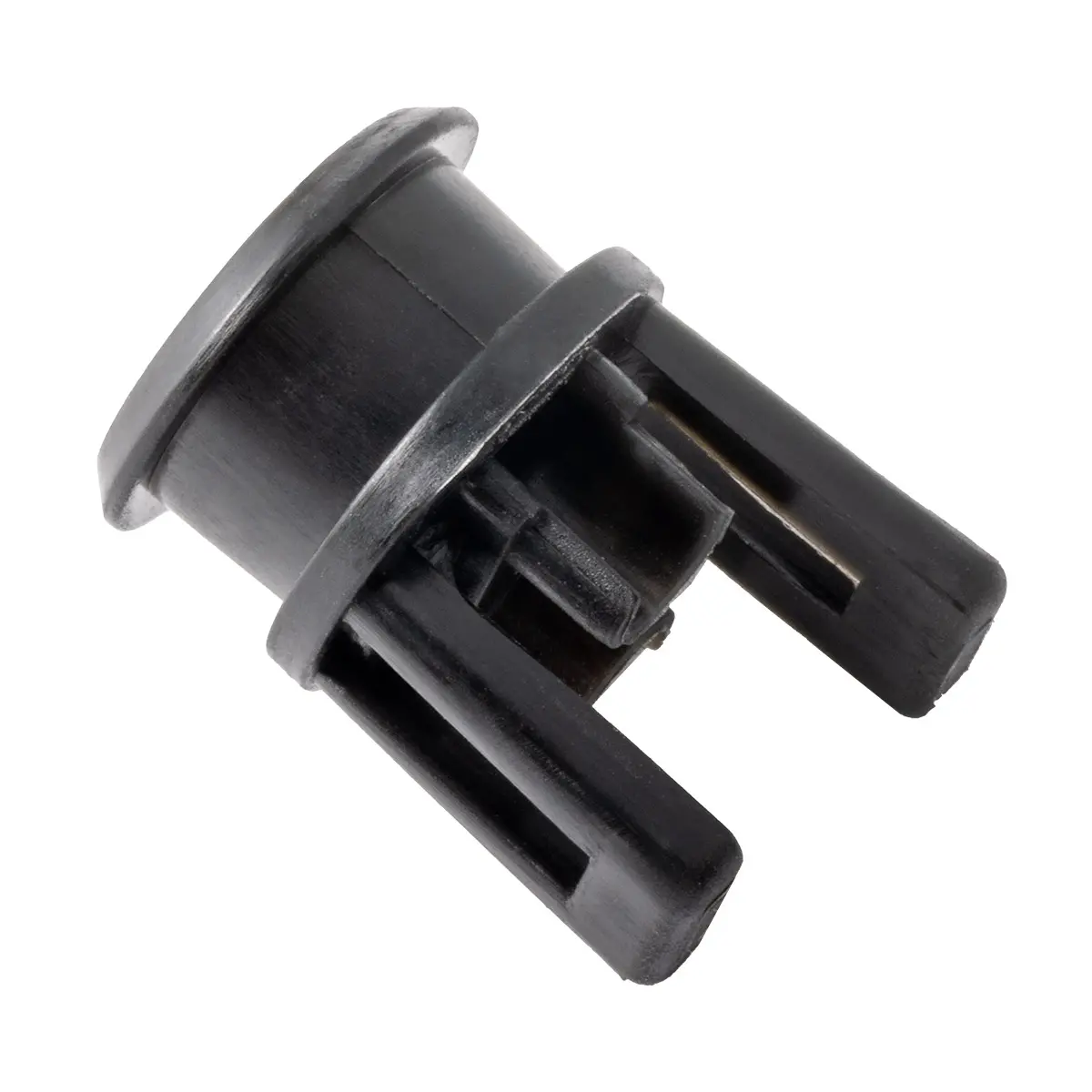
Boot: https://www.prowireusa.com/90-degree-ru ... ector.html
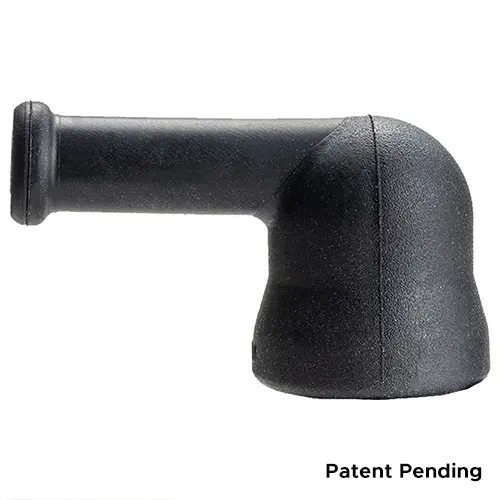
There is *ALSO* a GT150 triangular 3 cavity connector which Aptiv themselves make with a booting lip:
https://www.prowireusa.com/p-553-3-way- ... t-lip.html
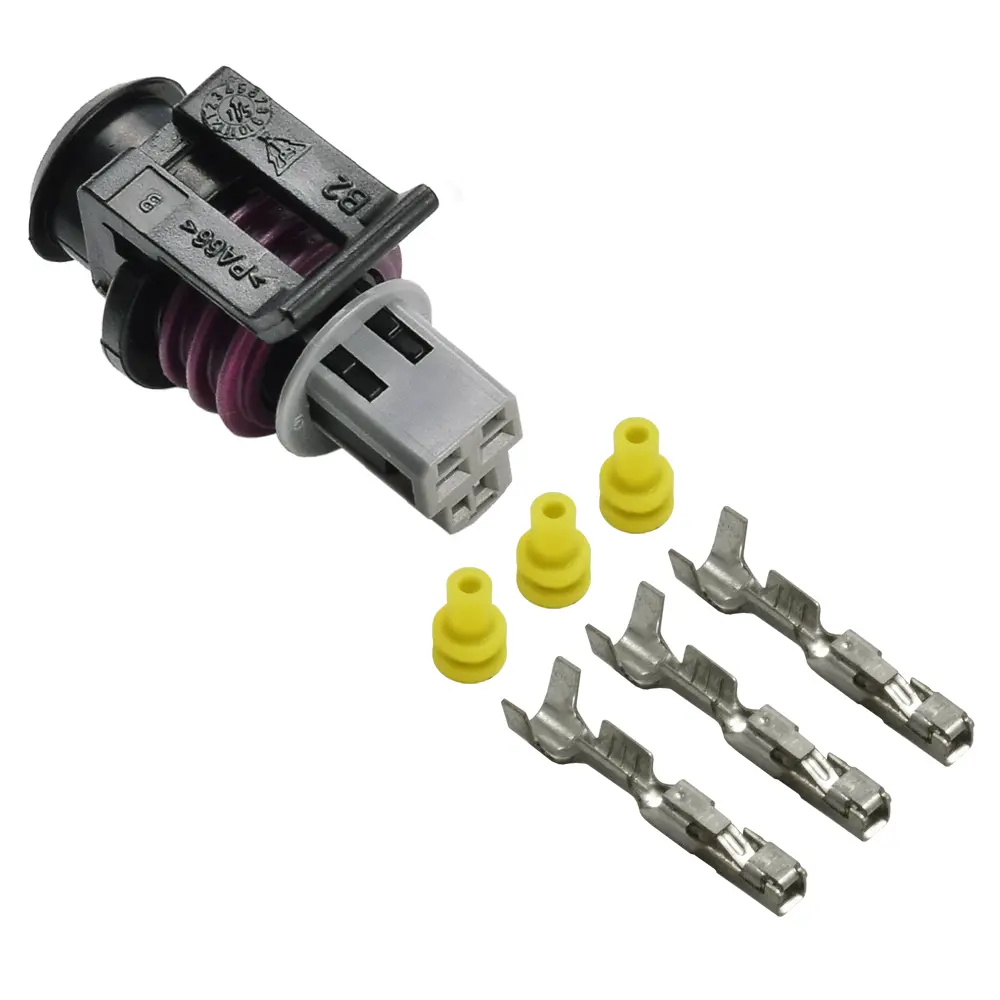
So I ordered the Aptiv injector connectors, the ProWire TPA, the Aptiv triangular connectors and enough boots for everything. I have an ECM oil pressure transducer, an aftermarket oil pressure transducer for logging, the GM 3 wire CTS that works with an ECM *AND* an analog gauge, and the AC pressure transducer... So I needed 12 boots and four triangular connectors.
The GT150 triangular connectors are PUSH-to-seat, while the Metri-pack 150 triangular connectors are pull-to-seat, with all the pain, suffering and fussiness that entails. I originally selected the MP150 part, wrote the wire list and had the spreadsheet build my BOM before I really understood the difference. Once I built one of the pull-to-seat MP150 connectors and understood that, I didn't even need an excuse to get rid of them.
To build with this boot:

After (Still note the text):

Service loops (I wound both of these the wrong direction, but they still work):


Service loops inside the boot:

TPA: https://www.prowireusa.com/TPA-EV14
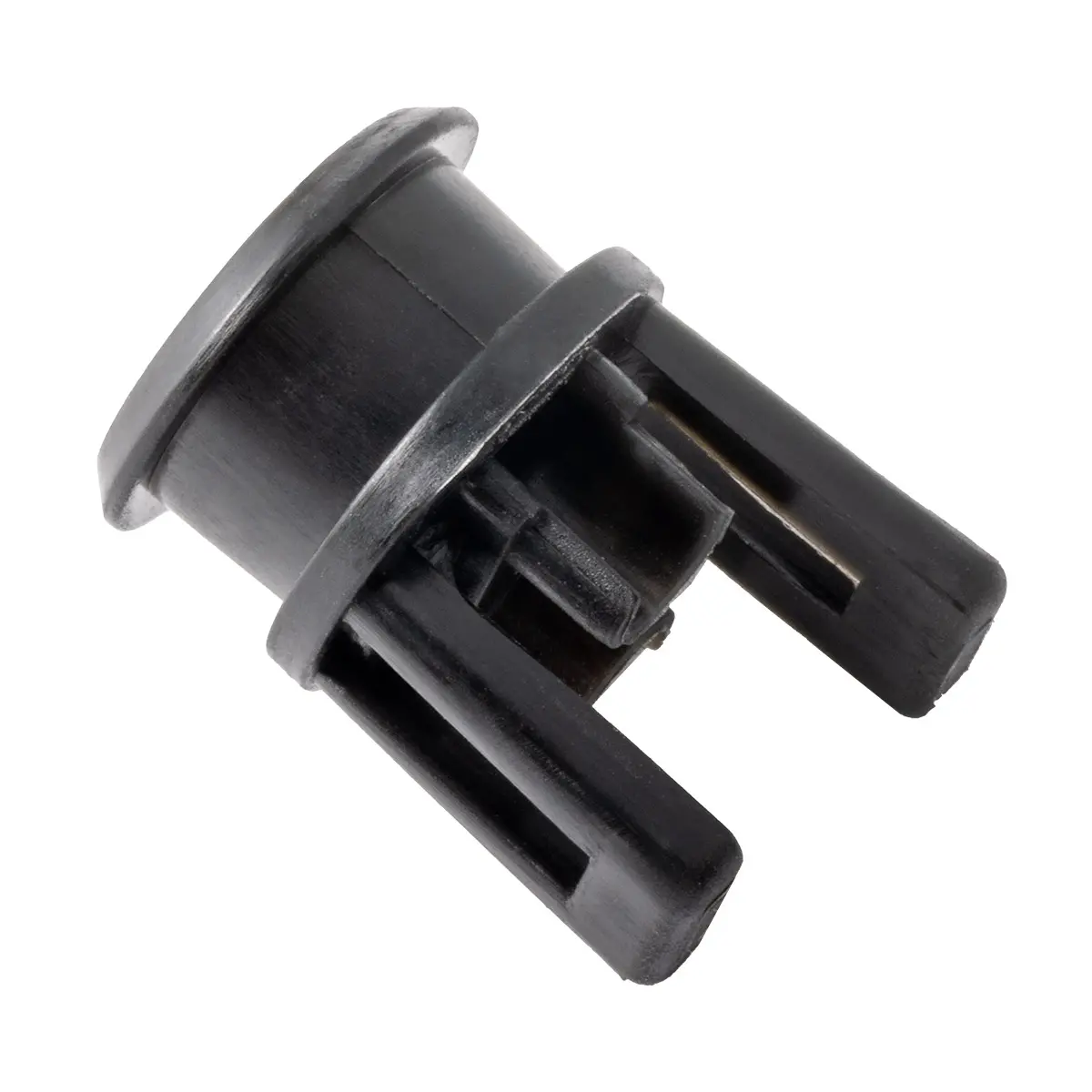
Boot: https://www.prowireusa.com/90-degree-ru ... ector.html
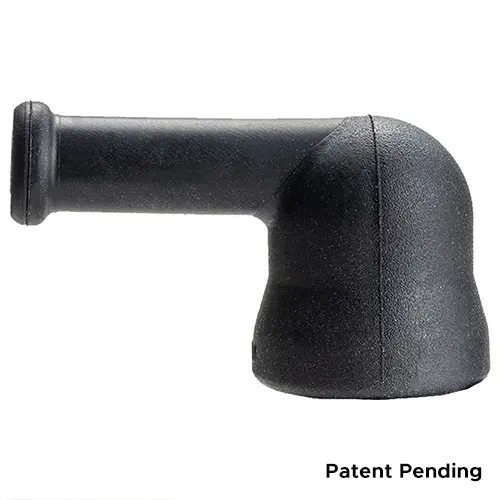
There is *ALSO* a GT150 triangular 3 cavity connector which Aptiv themselves make with a booting lip:
https://www.prowireusa.com/p-553-3-way- ... t-lip.html
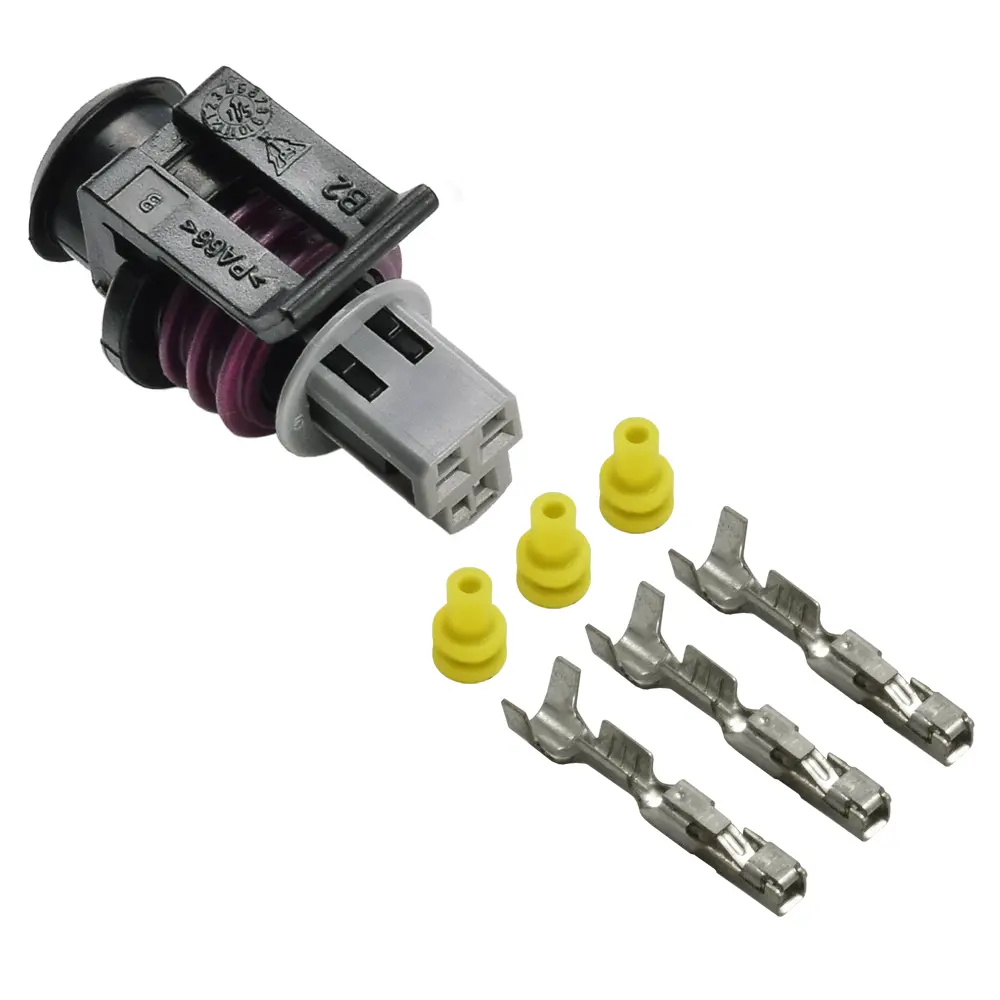
So I ordered the Aptiv injector connectors, the ProWire TPA, the Aptiv triangular connectors and enough boots for everything. I have an ECM oil pressure transducer, an aftermarket oil pressure transducer for logging, the GM 3 wire CTS that works with an ECM *AND* an analog gauge, and the AC pressure transducer... So I needed 12 boots and four triangular connectors.
The GT150 triangular connectors are PUSH-to-seat, while the Metri-pack 150 triangular connectors are pull-to-seat, with all the pain, suffering and fussiness that entails. I originally selected the MP150 part, wrote the wire list and had the spreadsheet build my BOM before I really understood the difference. Once I built one of the pull-to-seat MP150 connectors and understood that, I didn't even need an excuse to get rid of them.
To build with this boot:
- feed the wires through the boot
- Install the wire seals, strip the wire and crimp the contact, then crimp the wire seal
- install the terminals into the connector body
- Install the boot to the connector booting lip
- Shrink your DR-25 so that 3/4-7/8" of wire is bare between the end of the boot and the end of the shrink tube
- Peel the boot off the lip and slide it back so the small end of the boot slips onto the shrink tube.
- Make small service loops in the wires
- Install the boot back to the connector over the service loops. The wire used in the service loop pulls the shrink tube closer to the connector so that now the shrink tube and boot overlap

After (Still note the text):

Service loops (I wound both of these the wrong direction, but they still work):


Service loops inside the boot:

-
- Peer Mediator
- Posts: 15750
- Joined: Wed Nov 24, 2004 11:13 pm
- Location: In the darkness, where fear and knowing are one
- Contact:
Re: The Mule rides again (sort of) - pics.
This was listed erroneously for 2007 Grand Cherokee diesels, but may be useful for The Mule.
https://www.rockauto.com/en/moreinfo.ph ... 9&jsn=1948
https://www.rockauto.com/en/moreinfo.ph ... 9&jsn=1948
-
- Posts: 3082
- Joined: Mon May 24, 2010 5:34 pm
- Location: Aiken, SC
Re: The Mule rides again (sort of) - pics.
Wiring looks great!
I would highly recommend revising the bracket to just use a later model alternator that's readily available with the decouple pulley.
The Dark Side of Will wrote: ↑Sun Feb 02, 2025 5:44 pm
Thus I am constantly somewhat on the lookout for a decoupled alternator pulley in order run a softer tensioner on The Mule, and for the tensioner itself.
I would highly recommend revising the bracket to just use a later model alternator that's readily available with the decouple pulley.
"I am not what you so glibly call to be a civilized man. I have broken with society for reasons which I alone am able to appreciate. I am therefore not subject to it's stupid laws, and I ask you to never allude to them in my presence again."
-
- Peer Mediator
- Posts: 15750
- Joined: Wed Nov 24, 2004 11:13 pm
- Location: In the darkness, where fear and knowing are one
- Contact:
Re: The Mule rides again (sort of) - pics.
Re-homing the first post about concentric twisting because I realized I forgot to post info about injector wiring.
I also re-wrote this post to better describe my own design methodology for harness layers.
I've made significant progress on The Mule's wiring as I've been learning how to build a concentrically twisted harness.
OEMs, or at least GM, tend to use split convoluted tubing to sheathe harnesses. This make branch points trivial, since, even with just a one- or two-wire branch, the branching wires can just slip out of the split convoluted tubing wherever they need to. The branch point gets taped to ensure it doesn't come further apart and that's that.
Fancier harness construction methods, like sheathing with a nylon braid or DR-25 instead of spit convoluted tubing, benefit from more planning of the branch points. While it's still *possible* to build a DR-25 sheathed harness with the same topology as the OE harness, that becomes a fussy exercise in cutting, sequencing and shrinking short pieces of large diameter shrink tube to accommodate frequent branch points. The situation is even worse with a nylon braid, since using the braid for trunks requires dressing branch points with RayChem SCL or similar adhesive-lined shrink tube. While the braid *can* be spread to pass a wire through, this creates a potential chafe point for both braid and wire.
The fanciest harness construction method is concentric twisting. This method is defined in MIL-STD-339, which was deprecated and re-issued as MIL-HDBK-508. The authoritative source to download the document is here: https://quicksearch.dla.mil/qsDocDetail ... ber=203296
This method *requires* extensive planning of branch points, since layering and twisting the trunks in between is a very "constrained" operation... only so many ways of doing it work. This document includes tabulated and descriptive information on how to plan twisted layers so that they "work" when building the harness. One of the major considerations is the relationship between the bundle diameter and the number of wires used, which determines the "lay length" or axial length of harness required for the twisted layer to make a complete revolution. This trades inversely with "twist angle"... the steeper the twist angle, the shorter the lay length.
I also took High Performance Academy's online classes in Introduction, Club Sport and Motorsport Wiring, which is mostly based on MIL-STD-339.
I "tailored" the usual methods of motorsport wiring as follows:
-Aptiv (formerly Delphi) connectors for my GM sensors and actuators
-TXL wire rather than Tefzel
-Nested shrink tube at branch points rather than Raychem SCL or formed branch boots
-I use mixed-AWG layers of 18, 20 and 22ga, while most documentation assumes each layer consists of all the same gauge wires.
Installing a Northstar in a Fiero without rewiring the car is a collection of bad options
From the original ECM location, the harness can go through the original pass-through location in the firewall. The layout of the Northstar engine means that the immediate choice is to drape over the waterpump belt drive or route above the exhaust manifold. To help keep the harness from being conspicuous, I chose to route it above the exhaust manifold. I'll be using fire sleeving and probably making a sheet metal heat shield. The harness will turn around the front of the engine and route above the accessory belt drive, then wrap around the rear bank, again above and exhaust manifold. The last leg wraps around the bellhousing end of the engine and ducks under the throttle body to reach the distal branch point.
I started building this harness completely backwards in that I'm working from the distal branch point back toward the ECM.
The distal branch point is under the throttle body and configured with a "back branch" that exits the branch point next to the trunk that goes into the branch point. This branch point splits the trunk into the forward branches: Forward bank injectors (8 wires), MAP (3), DBW throttle (6); and the rear branches: Rear bank injectors (8), MAF (5). The branch point also contains two splices which split two injector feed wires into 8 injector power wires. I used stepped butt splices for this. Two 20ga injector power wires in the small end of the splice as the "forward" branch and the 16ga injector feed wire plus the other two 20ga injector power wires as the "back" branch in the large end of the splice.
I used the "Cadillac Style" injector wiring from '90's Northstars which bundles the end injectors of one bank with the middle pair of the other bank. This contrasts with GM's current method of putting each bank on its own feed. The old Cadillac method reduces peak current in the injector feed because not as many injectors in each feed are energized at the same time.
Here's setting up the injector power wires for splicing

A little in-process action:

The injector wires forming the first component of the branch point. I looped the rear bank injector signal wires around the bundle in order to keep the bend radius large enough to avoid damaging the wires.

And here it is ready to get started twisting the core and first layer:

I twisted the two 16ga injector feed wires together to form the core of my harness. Since there are only two wires, the major diameter of the core is twice the diameter of a 16ga txl wire, or 0.178. The minor diameter is the diameter of a single 16ga txl wire or 0.089. Averaging these two gives a bundle diameter of 0.134. This probably underestimates the working bundle diameter, since the 20ga wires in the first layer are not going to lie in the gaps between the 16ga wires. The result is that I did not use enough wires in the first layer, which results in a steeper twist angle, shorter lay length and use of more linear feet of wire than otherwise.
The first layer over the core consists of the eight 20ga injector signal wires. A ninth wire would have resulted in a shallower twist angle and a longer lay length, but I didn't have a ninth wire. I could have used a filler wire, but since this was the first layer I twisted, I didn't realize it wasn't very optimal.
One of the big frustrations of hand twisting a layer is that as you twist each wire, it's trying to spin around its own axis, resulting in all the adjacent wires twisting together at their far ends and becoming tangled. Thus every 1-3 revolutions you twist, you need to comb out EACH WIRE to prevent all the wires from tangling together, causing you to swear. I cite the range 1-3 because early in the process when the untwisted remainder of the wire is very long, you don't have to comb the bundle out as often. Later in the process when the remaining length is shorter you have to comb it out more often.
The finished diameter of the first layer is ~0.315 with a lay length of ~1.2. This results in a lay length to diameter ratio of 3.8, which is below the lower limit of the range recommended in MIL-HDBK-508.


After I took this photo, I twisted the remainder of the core and first layer to go all the way around the engine.
The second layer consists of The DBW Throttle (6), MAF (5) & MAP (3) wires, totaling 14. The DBW TAC wires (2) and MAF ground are 18 ga, the MAF +12V power is 20ga; all others are 22ga. This count is on the low side, but I didn't have any more wires.
The finished diameter of the second layer is ~0.450 with a lay length of ~1.8, for a ratio of 4. This is still below the recommended range.
The second layer looks like one of those giant ugly candy canes from the '80's or '90's:


While the twist angle is steep and the lay length is short... I still didn't have any other wires to add. However, just around the corner of the rear cylinder head will be the 2nd-to-last branch point. I can use some of the wires that join the harness to add to this second layer to increase the lay length and reduce the twist angle.
Because the part of the harness between the throttle body and 2nd-to-last branch point at the corner of the rear cylinder head will be visible with the engine in the car, I sheathed that portion with clear RT-375 so that I could show off my work and those who see it and know what a concentrically twisted harness is would be impressed. Since the finished diameter was 0.450, 3/4" RT-375 was the right size to use.

In order to add not-previously-planned wires to the second layer, I had to unwind the second layer. Unwinding a layer completely probably isn't as much of a PITA as winding it in the first place, but then rewinding it would be.
So I invented a way to unwind the layer just enough for rework, without unwinding it all the way.

That's just 3/4" PVC pipe

The zip-tied wires are NOT the ones I ended up adding, but this is a good shot of the end of the RT-375

And here's the final 2nd layer product, adding 3x 22ga wires from one of the oil pressure transducers into the layer.

You can see the difference in the twist angle and lay length. The new lay length is ~3.72, while the diameter remains 0.450. This yields a lay-length to diameter ratio of 8.27, which is just above the lower bound of the recommended range.

The design flow of MIL-HDBK-508 is to measure the diameter of the underlying layer, divide by the diameter of the wires to be used in the next layer and look up that ratio in a table in the document to find the suggested number of wires for the next layer.
In taking my first stab at designing my layers, I had used this table:

It came from a reputable source, though I have since asked for attribution.
This table seems to under-estimate the wire count for each layer compared to the MIL-HDBK-508. Also, my mixed-gauge layers and coarse-twist on the two wire core throw the numbers off a little bit as well.
This table is handy for TXL wire diameter: https://www.crimpzone.com/txl-wire-specification/
To rework my second layer per MIL-HDBK-508, I should have added 4 wires. I tried adding 2x 18ga for the backup lights and 2x 22ga for the VSS together. In trying to get that to lie well in a twist, I kept having one wire pop out when I squeezed all the others against the first layer. That was too many wires.
So after trying to add 2x 18ga + 2x 22ga and finding that didn't work, I tried 4x 22ga; that was better but didn't quite work either.
Going down to 3x 22ga added wires, finally worked.
I was able to wind that tightly over the first layer. The finished diameter was the same at 0.450, but the lay length stretched out to 3.72, for a lay length to diameter ratio of 8.27, which is within the recommended range.
So I went from 14 wires in the second layer with a much too short lay length of 1.8 to 17 wires in the second layer with a lay length of 3.72, or more than twice the lay length of my initial combo. When the layer is close to full, lay length is very sensitive to exactly how full the layer is.
I developed my own design flow which, because I'm me, uses plenty of arithmetic. It's based on "centerline circumference" instead of a table look-up.
To develop the parameters for the next layer, count up the number of wires of each gauge in your intended next layer. Use the OD of each wire gauge to add up the diameters of all wires. This is the calculated perimeter. Divide this by the number of wires to find the "average diameter" of wires in this layer. Add this diameter to the diameter of the last completed layer and multiply by Pi. This sum is the centerline circumference.
As the calculated perimeter approaches the centerline circumference the lay length goes to infinity.
The first leg of my second layer has 14 wires with an average diameter of 0.066. This represents a calculated perimeter of 0.922. The diameter of the first layer is 0.315. With an average diameter of 0.066, the centerline circumference is 1.197. The difference between 1.197 and 0.922 is significant, which is why this layer has a short lay length and high twist angle. The diameter of this layer is 0.450. With a lay length of 1.8, this results in a lay-length to diameter ratio of 4.
For the second leg, my first try added in 2x 18ga and 2x 22ga wires. This combination has a centerline circumference of 1.202 and a calculated perimeter of 1.200. This will not work because the centerline circumference is larger than the calculated perimeter.
My second try substituted 4x 22ga wires instead of the 2x 18ga dn 2x 22ga. This combination has a centerline circumference of 1.170 and a calculated perimeter of 1.194. While the centerline circumference is less than the calculated perimeter, it was not *ENOUGH* less than the calculated perimeter to account for any significant twist angle. This combo did not work.
My third try went down from 4x 22ga wires to 3x 22ga wires. This combination has a centerline circumference of 1.108 and a calculated perimeter of 1.194. The difference between these two numbers resulted in a lay length to diameter ratio of 8.27, which is at the bottom end of the recommended range. The diameter was still 0.450, while the lay length was 3.72.
My next step in developing this design flow is to account for twist angle in the centerline circumference, since the tangential component of circumference starts off at the wire diameter for a twist angle of zero and goes up as 1+sin(twist angle). The twist angle affects the centerline circumference. The lay length and centerline circumference are related by Pythagoras' theorem. The square root of the sum of the squares of the lay length and centerline circumference is the wire length of one revolution.
I've been coy about what the "recommended range" of lay length to diameter ratio actually is because... what's in 508 doesn't make sense in light of my very limited experience.
The "recommended range" per MIL-HDBK-508 section 600.3.5 is that the lay length of a layer be 8-12 times the finished diameter of that layer. My rework of my second layer showed that it will not lie correctly--that is, with all 2nd layer conductors lying firmly against the first layer--with even one more 22ga wire. The maximum diametral sum that can possibly fit results in a lay length to diameter ratio of 8.27... just barely into the bottom of the recommended range. I don't know how I'd go for a ratio any larger than what I achieved.
I also re-wrote this post to better describe my own design methodology for harness layers.
I've made significant progress on The Mule's wiring as I've been learning how to build a concentrically twisted harness.
OEMs, or at least GM, tend to use split convoluted tubing to sheathe harnesses. This make branch points trivial, since, even with just a one- or two-wire branch, the branching wires can just slip out of the split convoluted tubing wherever they need to. The branch point gets taped to ensure it doesn't come further apart and that's that.
Fancier harness construction methods, like sheathing with a nylon braid or DR-25 instead of spit convoluted tubing, benefit from more planning of the branch points. While it's still *possible* to build a DR-25 sheathed harness with the same topology as the OE harness, that becomes a fussy exercise in cutting, sequencing and shrinking short pieces of large diameter shrink tube to accommodate frequent branch points. The situation is even worse with a nylon braid, since using the braid for trunks requires dressing branch points with RayChem SCL or similar adhesive-lined shrink tube. While the braid *can* be spread to pass a wire through, this creates a potential chafe point for both braid and wire.
The fanciest harness construction method is concentric twisting. This method is defined in MIL-STD-339, which was deprecated and re-issued as MIL-HDBK-508. The authoritative source to download the document is here: https://quicksearch.dla.mil/qsDocDetail ... ber=203296
This method *requires* extensive planning of branch points, since layering and twisting the trunks in between is a very "constrained" operation... only so many ways of doing it work. This document includes tabulated and descriptive information on how to plan twisted layers so that they "work" when building the harness. One of the major considerations is the relationship between the bundle diameter and the number of wires used, which determines the "lay length" or axial length of harness required for the twisted layer to make a complete revolution. This trades inversely with "twist angle"... the steeper the twist angle, the shorter the lay length.
I also took High Performance Academy's online classes in Introduction, Club Sport and Motorsport Wiring, which is mostly based on MIL-STD-339.
I "tailored" the usual methods of motorsport wiring as follows:
-Aptiv (formerly Delphi) connectors for my GM sensors and actuators
-TXL wire rather than Tefzel
-Nested shrink tube at branch points rather than Raychem SCL or formed branch boots
-I use mixed-AWG layers of 18, 20 and 22ga, while most documentation assumes each layer consists of all the same gauge wires.
Installing a Northstar in a Fiero without rewiring the car is a collection of bad options

I started building this harness completely backwards in that I'm working from the distal branch point back toward the ECM.
The distal branch point is under the throttle body and configured with a "back branch" that exits the branch point next to the trunk that goes into the branch point. This branch point splits the trunk into the forward branches: Forward bank injectors (8 wires), MAP (3), DBW throttle (6); and the rear branches: Rear bank injectors (8), MAF (5). The branch point also contains two splices which split two injector feed wires into 8 injector power wires. I used stepped butt splices for this. Two 20ga injector power wires in the small end of the splice as the "forward" branch and the 16ga injector feed wire plus the other two 20ga injector power wires as the "back" branch in the large end of the splice.
I used the "Cadillac Style" injector wiring from '90's Northstars which bundles the end injectors of one bank with the middle pair of the other bank. This contrasts with GM's current method of putting each bank on its own feed. The old Cadillac method reduces peak current in the injector feed because not as many injectors in each feed are energized at the same time.
Here's setting up the injector power wires for splicing

A little in-process action:

The injector wires forming the first component of the branch point. I looped the rear bank injector signal wires around the bundle in order to keep the bend radius large enough to avoid damaging the wires.

And here it is ready to get started twisting the core and first layer:

I twisted the two 16ga injector feed wires together to form the core of my harness. Since there are only two wires, the major diameter of the core is twice the diameter of a 16ga txl wire, or 0.178. The minor diameter is the diameter of a single 16ga txl wire or 0.089. Averaging these two gives a bundle diameter of 0.134. This probably underestimates the working bundle diameter, since the 20ga wires in the first layer are not going to lie in the gaps between the 16ga wires. The result is that I did not use enough wires in the first layer, which results in a steeper twist angle, shorter lay length and use of more linear feet of wire than otherwise.
The first layer over the core consists of the eight 20ga injector signal wires. A ninth wire would have resulted in a shallower twist angle and a longer lay length, but I didn't have a ninth wire. I could have used a filler wire, but since this was the first layer I twisted, I didn't realize it wasn't very optimal.
One of the big frustrations of hand twisting a layer is that as you twist each wire, it's trying to spin around its own axis, resulting in all the adjacent wires twisting together at their far ends and becoming tangled. Thus every 1-3 revolutions you twist, you need to comb out EACH WIRE to prevent all the wires from tangling together, causing you to swear. I cite the range 1-3 because early in the process when the untwisted remainder of the wire is very long, you don't have to comb the bundle out as often. Later in the process when the remaining length is shorter you have to comb it out more often.
The finished diameter of the first layer is ~0.315 with a lay length of ~1.2. This results in a lay length to diameter ratio of 3.8, which is below the lower limit of the range recommended in MIL-HDBK-508.


After I took this photo, I twisted the remainder of the core and first layer to go all the way around the engine.
The second layer consists of The DBW Throttle (6), MAF (5) & MAP (3) wires, totaling 14. The DBW TAC wires (2) and MAF ground are 18 ga, the MAF +12V power is 20ga; all others are 22ga. This count is on the low side, but I didn't have any more wires.
The finished diameter of the second layer is ~0.450 with a lay length of ~1.8, for a ratio of 4. This is still below the recommended range.
The second layer looks like one of those giant ugly candy canes from the '80's or '90's:


While the twist angle is steep and the lay length is short... I still didn't have any other wires to add. However, just around the corner of the rear cylinder head will be the 2nd-to-last branch point. I can use some of the wires that join the harness to add to this second layer to increase the lay length and reduce the twist angle.
Because the part of the harness between the throttle body and 2nd-to-last branch point at the corner of the rear cylinder head will be visible with the engine in the car, I sheathed that portion with clear RT-375 so that I could show off my work and those who see it and know what a concentrically twisted harness is would be impressed. Since the finished diameter was 0.450, 3/4" RT-375 was the right size to use.

In order to add not-previously-planned wires to the second layer, I had to unwind the second layer. Unwinding a layer completely probably isn't as much of a PITA as winding it in the first place, but then rewinding it would be.
So I invented a way to unwind the layer just enough for rework, without unwinding it all the way.

That's just 3/4" PVC pipe

The zip-tied wires are NOT the ones I ended up adding, but this is a good shot of the end of the RT-375

And here's the final 2nd layer product, adding 3x 22ga wires from one of the oil pressure transducers into the layer.

You can see the difference in the twist angle and lay length. The new lay length is ~3.72, while the diameter remains 0.450. This yields a lay-length to diameter ratio of 8.27, which is just above the lower bound of the recommended range.

The design flow of MIL-HDBK-508 is to measure the diameter of the underlying layer, divide by the diameter of the wires to be used in the next layer and look up that ratio in a table in the document to find the suggested number of wires for the next layer.
In taking my first stab at designing my layers, I had used this table:

It came from a reputable source, though I have since asked for attribution.
This table seems to under-estimate the wire count for each layer compared to the MIL-HDBK-508. Also, my mixed-gauge layers and coarse-twist on the two wire core throw the numbers off a little bit as well.
This table is handy for TXL wire diameter: https://www.crimpzone.com/txl-wire-specification/
To rework my second layer per MIL-HDBK-508, I should have added 4 wires. I tried adding 2x 18ga for the backup lights and 2x 22ga for the VSS together. In trying to get that to lie well in a twist, I kept having one wire pop out when I squeezed all the others against the first layer. That was too many wires.
So after trying to add 2x 18ga + 2x 22ga and finding that didn't work, I tried 4x 22ga; that was better but didn't quite work either.
Going down to 3x 22ga added wires, finally worked.
I was able to wind that tightly over the first layer. The finished diameter was the same at 0.450, but the lay length stretched out to 3.72, for a lay length to diameter ratio of 8.27, which is within the recommended range.
So I went from 14 wires in the second layer with a much too short lay length of 1.8 to 17 wires in the second layer with a lay length of 3.72, or more than twice the lay length of my initial combo. When the layer is close to full, lay length is very sensitive to exactly how full the layer is.
I developed my own design flow which, because I'm me, uses plenty of arithmetic. It's based on "centerline circumference" instead of a table look-up.
To develop the parameters for the next layer, count up the number of wires of each gauge in your intended next layer. Use the OD of each wire gauge to add up the diameters of all wires. This is the calculated perimeter. Divide this by the number of wires to find the "average diameter" of wires in this layer. Add this diameter to the diameter of the last completed layer and multiply by Pi. This sum is the centerline circumference.
As the calculated perimeter approaches the centerline circumference the lay length goes to infinity.
The first leg of my second layer has 14 wires with an average diameter of 0.066. This represents a calculated perimeter of 0.922. The diameter of the first layer is 0.315. With an average diameter of 0.066, the centerline circumference is 1.197. The difference between 1.197 and 0.922 is significant, which is why this layer has a short lay length and high twist angle. The diameter of this layer is 0.450. With a lay length of 1.8, this results in a lay-length to diameter ratio of 4.
For the second leg, my first try added in 2x 18ga and 2x 22ga wires. This combination has a centerline circumference of 1.202 and a calculated perimeter of 1.200. This will not work because the centerline circumference is larger than the calculated perimeter.
My second try substituted 4x 22ga wires instead of the 2x 18ga dn 2x 22ga. This combination has a centerline circumference of 1.170 and a calculated perimeter of 1.194. While the centerline circumference is less than the calculated perimeter, it was not *ENOUGH* less than the calculated perimeter to account for any significant twist angle. This combo did not work.
My third try went down from 4x 22ga wires to 3x 22ga wires. This combination has a centerline circumference of 1.108 and a calculated perimeter of 1.194. The difference between these two numbers resulted in a lay length to diameter ratio of 8.27, which is at the bottom end of the recommended range. The diameter was still 0.450, while the lay length was 3.72.
My next step in developing this design flow is to account for twist angle in the centerline circumference, since the tangential component of circumference starts off at the wire diameter for a twist angle of zero and goes up as 1+sin(twist angle). The twist angle affects the centerline circumference. The lay length and centerline circumference are related by Pythagoras' theorem. The square root of the sum of the squares of the lay length and centerline circumference is the wire length of one revolution.
I've been coy about what the "recommended range" of lay length to diameter ratio actually is because... what's in 508 doesn't make sense in light of my very limited experience.
The "recommended range" per MIL-HDBK-508 section 600.3.5 is that the lay length of a layer be 8-12 times the finished diameter of that layer. My rework of my second layer showed that it will not lie correctly--that is, with all 2nd layer conductors lying firmly against the first layer--with even one more 22ga wire. The maximum diametral sum that can possibly fit results in a lay length to diameter ratio of 8.27... just barely into the bottom of the recommended range. I don't know how I'd go for a ratio any larger than what I achieved.
-
- Peer Mediator
- Posts: 15750
- Joined: Wed Nov 24, 2004 11:13 pm
- Location: In the darkness, where fear and knowing are one
- Contact:
Re: The Mule rides again (sort of) - pics.
Looking great is why I'm going through the ass-pain of doing it this wayericjon262 wrote: ↑Tue Feb 11, 2025 10:36 pm Wiring looks great!
The Dark Side of Will wrote: ↑Sun Feb 02, 2025 5:44 pm
Thus I am constantly somewhat on the lookout for a decoupled alternator pulley in order run a softer tensioner on The Mule, and for the tensioner itself.
I would highly recommend revising the bracket to just use a later model alternator that's readily available with the decouple pulley.

I've just updated the bracket to slightly move the tensioner so that the tensioner bolt clears the battery tray as I remove it.
Changing alternator AND tensioner will require a lot more thought and a bunch of trial and error with belt length. I'll leave that for Future William... that dude seems to be able to get shit done.
-
- Peer Mediator
- Posts: 15750
- Joined: Wed Nov 24, 2004 11:13 pm
- Location: In the darkness, where fear and knowing are one
- Contact:
Re: The Mule rides again (sort of) - pics.
So far I've covered that I twisted the core of 2x 16ga injector feeds, then wound the first layer of 8x 20ga injector signal wires.
The second layer had two legs. The first leg ran from the distal branch point to the next-to-last branch point and consisted of 3x 18ga, 1x 20ga and 10x 22ga. The second leg added 3x 22ga wires to consist of 3x 18ga, 1x 20ga and 13x 22ga.
Here's a photo of the second leg in process. I added the 3x 22ga wires from the ECM oil pressure transducer. I left way too much at the connector end because I hadn't fully dressed and routed it at this point. That's ok... with careful work, all that slack can be pulled through the twist so as not to waste wire.

After building a couple of twisted layers and evaluating the results, I'm getting into the third layer with some idea of what I'm doing.
The third layer starts where the second layer changes from its first leg to its second leg.
The third layer will also have two legs.
The first leg consists of Bank 2 Coils (7), Oil Pressure Logger (3), Coolant Temp & Gauge (3), Back Up Lights (2) & Vehicle Speed Sensor (2).
This collection is 2x 16ga, 2x 18ga, 5x 20ga & 8x 22ga.
Here's a pic of wrapping service loops--in the correct direction this time--on one of the triangular 3 cavity connectors.

This collection has a calculated perimeter of 1.17 with an average diameter of 0.069
The finished second layer has an OD of 0.450, which with the average wire diameter of 0.069 results in a centerline circumference of 1.630.
The difference between 1.630 and 1.17 is WAY too large, and will result in a very steep twist angle and short lay length.
By adding 6x 22ga filler wires, I can bring the calculated perimeter to 1.542. The average diameter comes down to 0.067 and the centerline circumference to 1.624. This combination will work.
This results in a finished diameter of 0.580 and a lay length of 6", with a ratio of 10.34.
The 0.580 finished diameter requires 1" DR-25. I installed that with a resulting trunk diameter of 0.650-0.670. Since this is just under 11/16", I'll need 3/4" heat protective sleeve for this leg, since it passes above the exhaust manifold.
A few shots of that process:




The big tan stripe is my six filler wires
This leg complete

And with 1" DR-25


The back corner of the engine that will be visible in the engine bay does end up a bit cluttered... and obscures visibility of the trunk I sheathed in RT-375

The second leg removes the fillers and removes the Back Up Lights and temperature gauge wire, since those branch off to terminate in the C500 connector. In place of those 9 wires are Bank 1 Coils (7), Alternator L wire (1).
This leg consists of 4x 16ga, 10x 20ga, 8x 22ga. The calculated perimeter is 1.532 with an average diameter of 0.070. The centerline circumference is 1.634. This combo works as well as the first leg. Finished dimensions are essentially the same.
Since this leg will be visible by the battery, I installed 1" RT-375 instead of DR-25. The resulting trunk diameter is 0.625-0.630. My temporary Adel clamps for setup are 1.25 or so... I'll need to switch them for 5/8" Adel clamps for the finished product.
For the third leg of the harness overall...
The 6x 22ga filler wires just end, the 2x 18ga Back Up LIght wires come out and the 1x 22ga temperature gauge sender wire comes out. I replace them with 2x 16ga, 5x 20ga coil wires and 1x 22ga alternator L wire.

And just keep doing exactly the same twist after that:

and shrink 1" RT-375 over it, since this trunk will be visible with the engine installed



I am *FINALLY* at the point where I have the third leg of the harness COMPLETE.

I still have some branch point dressing to finish, and I need to dress and terminate the wires going to the C500--which requires the engine being in the car--but three of the four trunks are DONE. I am deciding if I can build a fourth layer for the fourth trunk, or if the remaining wires will just form a smaller parallel trunk.
The REAR (Bank 1) bank O2 sensor wires did not fit in the Layer 3 Leg 2 winding, so those four will run as a parallel bundle behind the main trunk to get to the next branch point.
Remaining wires to incorporate:
Bank 1 O2 (4), Valley Harness (10), Accessory Branch (15). 29 together is light for the diameter I have to twist now... but I still need to run the numbers to figure out how many fillers I might need. Valley harness consists of Crank Sensor (3), Cam Sensor (3), Bank 1 Knock Sensor (2) and Bank 2 Knock Sensor (2). Accessory Branch consists of Oil Pressure Sender/Switch (4), Oil Level Switch & Sump Temp (3), AC Pressure Transducer (3), AC Compressor Clutch (2), and Alternator (3).
I am also thinking about what I need to do with the red 8ga alternator output wire... it runs from the alternator output stud to the +12V junction block visible in the photo above... but it doesn't readily fit in any twist as anything but a core. I'll probably end up putting small split convoluted tubing on it by itself and running it next to the main harness. The purple 10ga crank wire needs some attention, but not as much. I have an MP480 disconnect for it. The disconnect will come out of C500 from the stock crank wire terminal. I ALSO have a 10ga wire to run inside the car to my fuse & relay module that holds the PWRTRN relay, AC Comp clutch relay & fuel pump relay, as well as the injector and coil fuses.
The second layer had two legs. The first leg ran from the distal branch point to the next-to-last branch point and consisted of 3x 18ga, 1x 20ga and 10x 22ga. The second leg added 3x 22ga wires to consist of 3x 18ga, 1x 20ga and 13x 22ga.
Here's a photo of the second leg in process. I added the 3x 22ga wires from the ECM oil pressure transducer. I left way too much at the connector end because I hadn't fully dressed and routed it at this point. That's ok... with careful work, all that slack can be pulled through the twist so as not to waste wire.

After building a couple of twisted layers and evaluating the results, I'm getting into the third layer with some idea of what I'm doing.
The third layer starts where the second layer changes from its first leg to its second leg.
The third layer will also have two legs.
The first leg consists of Bank 2 Coils (7), Oil Pressure Logger (3), Coolant Temp & Gauge (3), Back Up Lights (2) & Vehicle Speed Sensor (2).
This collection is 2x 16ga, 2x 18ga, 5x 20ga & 8x 22ga.
Here's a pic of wrapping service loops--in the correct direction this time--on one of the triangular 3 cavity connectors.

This collection has a calculated perimeter of 1.17 with an average diameter of 0.069
The finished second layer has an OD of 0.450, which with the average wire diameter of 0.069 results in a centerline circumference of 1.630.
The difference between 1.630 and 1.17 is WAY too large, and will result in a very steep twist angle and short lay length.
By adding 6x 22ga filler wires, I can bring the calculated perimeter to 1.542. The average diameter comes down to 0.067 and the centerline circumference to 1.624. This combination will work.
This results in a finished diameter of 0.580 and a lay length of 6", with a ratio of 10.34.
The 0.580 finished diameter requires 1" DR-25. I installed that with a resulting trunk diameter of 0.650-0.670. Since this is just under 11/16", I'll need 3/4" heat protective sleeve for this leg, since it passes above the exhaust manifold.
A few shots of that process:




The big tan stripe is my six filler wires
This leg complete

And with 1" DR-25


The back corner of the engine that will be visible in the engine bay does end up a bit cluttered... and obscures visibility of the trunk I sheathed in RT-375

The second leg removes the fillers and removes the Back Up Lights and temperature gauge wire, since those branch off to terminate in the C500 connector. In place of those 9 wires are Bank 1 Coils (7), Alternator L wire (1).
This leg consists of 4x 16ga, 10x 20ga, 8x 22ga. The calculated perimeter is 1.532 with an average diameter of 0.070. The centerline circumference is 1.634. This combo works as well as the first leg. Finished dimensions are essentially the same.
Since this leg will be visible by the battery, I installed 1" RT-375 instead of DR-25. The resulting trunk diameter is 0.625-0.630. My temporary Adel clamps for setup are 1.25 or so... I'll need to switch them for 5/8" Adel clamps for the finished product.
For the third leg of the harness overall...
The 6x 22ga filler wires just end, the 2x 18ga Back Up LIght wires come out and the 1x 22ga temperature gauge sender wire comes out. I replace them with 2x 16ga, 5x 20ga coil wires and 1x 22ga alternator L wire.

And just keep doing exactly the same twist after that:

and shrink 1" RT-375 over it, since this trunk will be visible with the engine installed



I am *FINALLY* at the point where I have the third leg of the harness COMPLETE.

I still have some branch point dressing to finish, and I need to dress and terminate the wires going to the C500--which requires the engine being in the car--but three of the four trunks are DONE. I am deciding if I can build a fourth layer for the fourth trunk, or if the remaining wires will just form a smaller parallel trunk.
The REAR (Bank 1) bank O2 sensor wires did not fit in the Layer 3 Leg 2 winding, so those four will run as a parallel bundle behind the main trunk to get to the next branch point.
Remaining wires to incorporate:
Bank 1 O2 (4), Valley Harness (10), Accessory Branch (15). 29 together is light for the diameter I have to twist now... but I still need to run the numbers to figure out how many fillers I might need. Valley harness consists of Crank Sensor (3), Cam Sensor (3), Bank 1 Knock Sensor (2) and Bank 2 Knock Sensor (2). Accessory Branch consists of Oil Pressure Sender/Switch (4), Oil Level Switch & Sump Temp (3), AC Pressure Transducer (3), AC Compressor Clutch (2), and Alternator (3).
I am also thinking about what I need to do with the red 8ga alternator output wire... it runs from the alternator output stud to the +12V junction block visible in the photo above... but it doesn't readily fit in any twist as anything but a core. I'll probably end up putting small split convoluted tubing on it by itself and running it next to the main harness. The purple 10ga crank wire needs some attention, but not as much. I have an MP480 disconnect for it. The disconnect will come out of C500 from the stock crank wire terminal. I ALSO have a 10ga wire to run inside the car to my fuse & relay module that holds the PWRTRN relay, AC Comp clutch relay & fuel pump relay, as well as the injector and coil fuses.